case study
Laboratory Management / Manufacturing
The Problem:
The client’s existing laboratory process was extremely labor intensive and required manual transcription of specifications and results across multiple systems.
They were utilizing an old software system to track samples/materials to be tested. Due to the outdated system’s limitations, the client had to use many paper forms daily to capture all data needed. All their specifications/inputs for concrete and steel specimens were on handwritten forms. Once the office received the handwritten forms, the specifications/inputs had to be entered into the computers that ran their machines. After that, all output data/results had to be handwritten onto forms, then transferred to the Legacy System. Results for other tests that the Legacy System did not support had to be manually typed into Word/PDF reports afterward.
These processes required a large load of administrative work on the client’s part to keep everything running. The big challenge was that their reporting had to be done at a pace close to real-time due to Materials Testing Guidelines and client contracts. The administrative process was lengthy and often delayed reporting, which did not allow our client to give the best possible customer service.
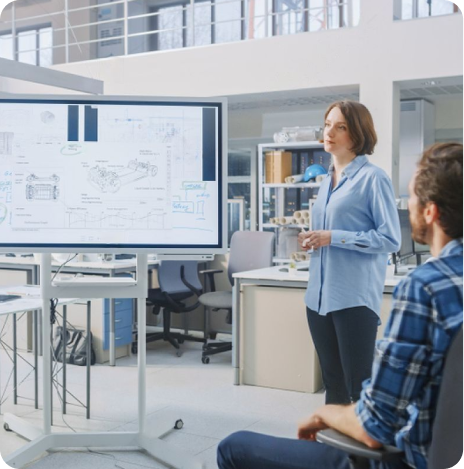
The Consulting Process
The Hawkins Consulting team engaged with leaders and stakeholders in the client’s Laboratory Department to gather data and requirements for the new system. We investigated their existing systems and workflows and specified the inputs and outputs needed in the Laboratory System.
We determined that the data from Client’s Field Sampling/Reporting System would flow into this system, then, data from laboratory tests would be entered into custom forms based on test type and code requirements. Final Reports would be automatically generated by the system to be sent to clients.
Part of this evaluation process was a detailed investigation of the integrations that would be required to allow the new software to work seamlessly with the client’s existing systems.
Finally, the client’s lab used 2 pieces of industrial testing machinery that our client wanted to interact with digitally and automatically. Previously all inputs and outputs were manually keyed in/transposed to paper for each test specimen.
All of these considerations and more factored into our proposal to digitize, streamline, and automate the client’s lab processes.
Roadmap of Implementation:
- Determined the most valuable functionality that would assist our client in automating 80% of their laboratory’s workload.
- Researched the laboratory testing specifications per state code and input them into the system.
- Developed a prototype with the client’s subject matter experts’ guidance.
- Delivered and live-tested the prototype with lab staff.
- Created training materials and process documentation.
- Ran demo sessions of the new software platform.
- Imported all data from the legacy system into this platform via a custom-built data integration program to ensure the integrity of the past 10+ years of data.
- Troubleshooting issues (after launch), providing ongoing consultation
- Deployed process improvements after launch working alongside clients’ staff to fine-tune the product

Development, Implementation, and Results:
Hawkins Team Developed and Implemented a web application for this client. This Web Application was built completely from scratch using PHP, MySQL, and Bootstrap as the core technologies. The platform’s web server was hosted on Microsoft Azure. All requirements gathering, design, development, testing, configuration, and deployment were done by the Hawkins Team.
Note: The Hawkins Team utilizes Agile/Scrum Software Development methodologies to deliver working prototypes and value early and often to test alongside their clients’ existing systems. From there the team iterates in coordination with their clients to shape and guide further development and improvements.
Through routine client demos, the Hawkins Team was able to provide valuable process improvements for the client’s end users. In this project, the software changed so much about how the laboratory employees do their day-to-day work and made significant reductions in redundant paperwork and data entry. The application is now used by all laboratory staff to:
- track all materials for testing
- approve incoming materials for testing
- log work-in-progress data
- produce reports when tests are complete
Reaction:
Management in the laboratory department was pleased with the efficiency improvements and consolidation of data because the changes reduced both their manual workload and day-to-day stressors. The end users benefitted from the same advantages and were led through training sessions on the new system for a seamless adoption of the technology.
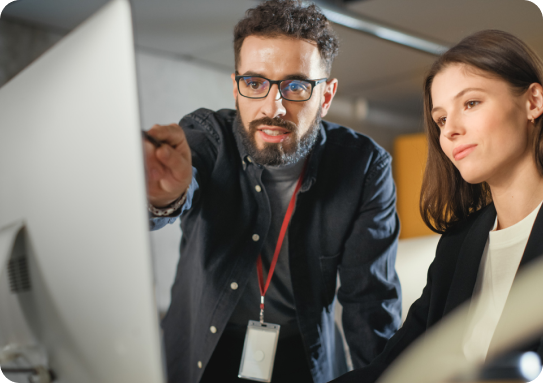
Time/Resources Saved
In addition to endless hours of labor saved in removing the outdated manual input processes, the laboratory staff now have a real-time connection to upcoming, current, and past test data and the laboratory staff can notify clients in real-time of any material test failures.
Business Impact
The client can now give better and more timely customer service utilizing an array of system-generated standardized laboratory reports that cover all required information per specific code requirements.